Inzago (MI), Italia
Da cosa nasce cosa: nulla di più banale eppure vero, anche nel mondo del lavoro e anche quando vengono chiamate in causa competenze tecniche ben precise. Lo sanno bene alla Bindellini, azienda situata ad Inzago, a est di Milano, attiva da oltre quarant'anni nel campo della progettazione e consulenza termotecnica e qualificata da un portafoglio competenze che coinvolge anche la realizzazione di impianti ad alta efficienza energetica (cogenerazione e trigenerazione).
Per la maggior parte, le applicazioni gestite da Bindellini riguardano la produzione di energia combinata (elettrica+termica); la qualità dell'applicazione è il focus principale dell'azienda, cosa che comporta il passaggio in secondo piano dei costi: risparmiare va bene, ma prima di pensare al risparmio occorre essere in grado di fare bene e garantire uno standard elevato.
Ma come si passa dalla termotecnica ad occuparsi della filatura di fibre polimeriche, due mondi apparentemente così lontani? A raccontarlo è Nicola Bindellini, amministratore e responsabile tecnico dell'azienda che porta il nome della sua famiglia. "Un nostro cliente, per il quale ci stavamo occupando della gestione termotecnica di un impianto, ci ha segnalato alcuni problemi inerenti la gestione fluidodinamica del processo produttivo, fino a quel momento condotto in maniera abbastanza approssimativa. Forti della nostra solida esperienza in ambito fluidodinamico, ci siamo proposti e abbiamo preso in carica l'amministrazione del processo di filatura".
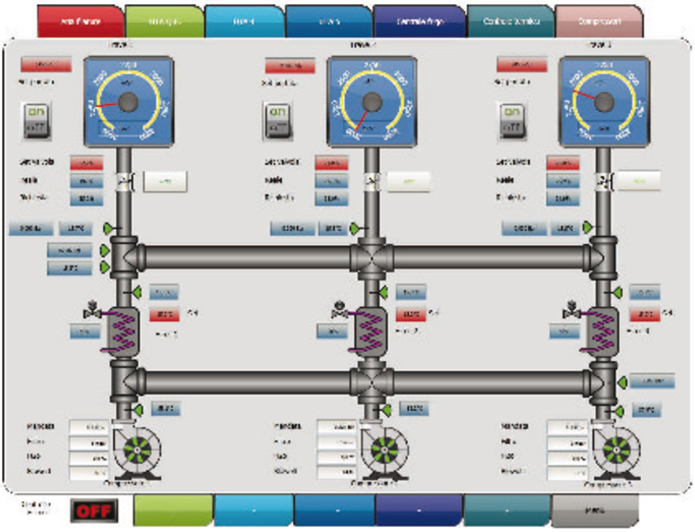
L’ottimizzazione delle prestazioni della mac china doveva pas sare per l’automazione di parte del processo, che fino ad allora era stato gestito manualmente.
Si tratta di un processo complicato (l’aria viene trattata in termini di pressione, temperatura e volume e mantenuta
a temperatura costante), che prima veniva controllato da un operatore, che si annotava i dati utili su un registro
con tutte le approssimazioni del caso.
Ora che la macchina è stata portata in una condizione di automazione non esiste più possibilità di errore: è tutto monitorato e memorizzato.
Linea produttiva ottimizzata significa un maggiore controllo dell’efficienza,affidabilità
- Intesisbox è pratico, i pannelli beijer intuitivi da usare
- Architettura con un “cuore” performante
- Investire in qualità per differenziarsi