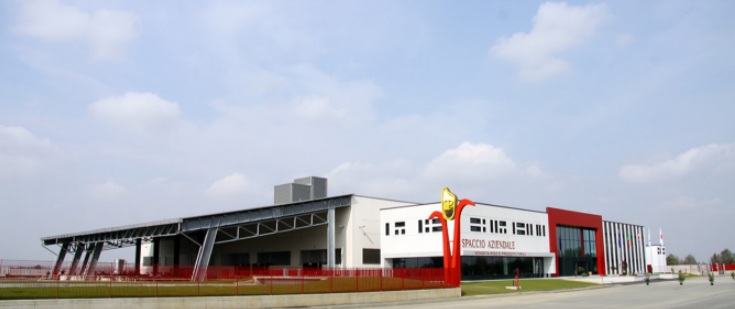
PROGETTO
Come risolvere in maniera semplice e innovativa le problematiche gestionali di ungrande impianto dedicato alla lavorazione del riso come quello di S.P.? Nel cuore deldistretto risicolo vercellese questa sfida è stata vinta brillantemente da Atec Sistemi,grazie a un’intuizione geniale che Ignition, il software di Inductive Automationdistribuito e supportato in Italia da EFA Automazione, ha permesso di trasformare in realtà.
Settore: Macchine e Impianti
Cliente: S.P. spa
Prodotto: Ignition
Stroppiana (VC) – Riconosciuto da più parti come il distretto…
Riconosciuto da più parti come il distretto risicolo d’eccellenza, il vercellese incarna una tradizione storico-culturale del territorio che va ben oltre le dimensioni produttive e le caratteristiche tipiche del settore, che rivestono comunque un rilievo che arriva ben oltre i confini nazionali. Proprio in quest’area caratterizzata da specializzazione produttiva e concentrazione di filiera, ha sede la S.P. basata a Stroppiana, in provincia di Vercelli. Il suo core business è la lavorazione e la venditadi riso (convenzionale e bio) sfuso e confezionato per conto terzi e la commercializzazione di proprie linee diprodotto.L’azienda, a conduzione familiare, ha saputo precorrere i tempi fino a diventare un leader nel proprio settore, cogliendo le nuove sfide e le opportunità del mercato. Parte del suo successo risiede anche nella continua volontà di ammodernare i propri impianti. Ed è qui che entra in gioco Atec Sistemi, system integrator che da anni è partner di EFA Automazione che si è occupato di affrontare e risolvere le problematiche di gestione della produzione all’interno della riseria.S.P., nello specifico, aveva l’esigenza di riorganizzare e ottimizzare la gestione dei propri impianti di produzione.
Così, con il supporto di Atec e il contributo di EFA Automazione, è nata l’idea di realizzare un innovativo sistema capace di gestire in maniera ottimale il workflow produttivo.
Come funziona una riseria?Ad arrivare in riseria per essere lavorato è ovviamente il prodotto grezzo che, dopo una prima operazione di pulizia, viene inviato in una serie di sili. La materia prima, ovvero il “risone”, classificata secondo le specifiche codificate dall’Ente Nazionale Risi in base alle miscele, alle tipologie e alle diverse qualità, deve essere avviata alle opportune lavorazioni: sbramatura/pulitura, sbiancatura, setacciamento ecc. Dopo essere giunto in altri sili di stoccaggio intermedio, il prodotto è pronto per il confezionamento, che può essere fatto in big bag, sacchi, sacchetti ecc. In realtà, prima del confezionamento, avviene ancheun’altra fase di lavorazione, che prevede il trattamento del riso con Co2 a 20 Bar all’interno di 3 sili verticali speciali. Tale fase può anche essere successiva, ovvero compiuta direttamente sul prodotto confezionato in sacchi, che allo scopo viene stoccato in apposite autoclavi di tipo orizzontale con trattamento fino a 30 Bar. In sostanza, questo trattamento provvede alla disinfestazione del prodotto conferendogli caratteristiche di lunga conservazione, il che assicura al consumatore finale che il riso, anche dopo un anno, mantenga inalterate le sueproprietà organolettiche. A questo punto il riso è pronto per essere caricato sui camion.
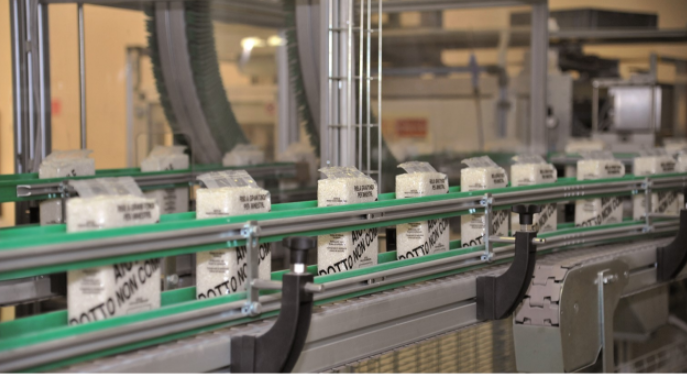
Il ruolo tecnologico di Atec Sistemi
In tutto questo complesso sistema di lavorazioni, qual è stato il ruolo di Atec Sistemi – il system integrator che ha
realizzato l’applicazione – e in che modo è riuscito a ottimizzare la gestione dei processi produttivi di S.P.?
“Poiché il prodotto deve subire diverse lavorazioni, immaginiamoci che all’interno dell’impianto il riso possa percorrere diverse strade, anche in contemporanea”, esordisce Mauro Ceriani, CEO di Atec Sistemi. “In fabbrica esiste una vera e propria ragnatela di percorsi che il riso può seguire: da qui è scaturita l’idea vincente. Il concetto a cui ci siamo ispirati è stato quello di ideare un sistema simile al navigatore che, tutti noi, quotidianamente utilizziamo sui nostri smartphone”.
Per andare da un punto all’altro, spiega Ceriani, vi è la possibilità di percorrere strade diverse: e infatti il naviga-tore ci chiede, prima di avviare il routing, quale percorso intendiamo scegliere. “Ecco, per S.P. abbiamo fatto la stessa cosa: all’operatore viene chiesto quale delle 6 bilance presenti nell’impianto intende usare per il trasferimento del prodotto e il sistema stabilisce il percorso che deve essere seguito per arrivare a destinazione”.
Il riso deve essere tracciato in modo completo e la bilancia ha uno scopo fondamentale. “Ipotizziamo di dover trasferire un lotto di riso da 500 tonnellate da un punto A ad un punto B: il sistema che abbiamo realizzato identifica le macchine disponibili per le lavorazioni, le seleziona e le propone all’operatore. A quest’ultimo, quindi, è data la facoltà di scegliere il percorso da seguire”, sottolinea Ceriani.Ebbene, questo meccanismo di “routing”, simile proprio alla logica di un comune navigatore, rappresenta il cuore del sistema di produzione, che dopo essere stato implementato, ha visto una lunga fase di test sul campo durata circa un anno. La conformazione dell’impianto su cui è stata implementata questa innovativa soluzione consente, in base alla disponibilità delle varie sezioni impiantistiche, di gestire 154 diverse ricette, ovvero
di poter scegliere tra 154 percorsi diversi su cui il prodotto potrebbe essere instradato in una delle sezioni principali.
Il generatore di rotte e di lotti
Il generatore di rotte ideato da Atec Sistemi permette dunque di trovare la via più breve per il trasporto del riso nell’impianto di produzione, che prevede diversi sili e molti macchinari per gli spostamenti. Lo stesso generatore di rotte, attraverso un’apposita interfaccia di gestione, viene anche utilizzato per gestire la produzione dei lotti.L’architettura si avvale di un PLC dedicato che funge da interfaccia del database, nonché da master per altri 7 PLC, al fine di coordinare il generatore di percorsi e gestire in modo consistente tutte le sezioni impiantistiche da impegnare nei vari passaggi. Tra le funzionalitàdel sistema vi sono anche quelle che attengono al monitoraggio dei sistemi di pesatura, che rilevano la quantità di materiale che viaggia tra le varie parti dell’impianto. Questa architettura consente di rilevare efficacemente e in modo univoco tutte le informazioni sui lotti di produzione, archiviandole nel database.
“Il generatore di rotte è il cuore del sistema che abbiamo sviluppato per S.P. e si trova installato su tutti gli 8 PLC dell’impianto. Il sistema di supervisione, che si coordina con i PLC installati sul campo, integra un database di produzione, all’interno del quale confluiscono i dati di processo che, lo stesso sistema, rende disponibili a un gestionale esterno di livello più elevato”, precisa Ceriani.
Il ruolo di Ignition
Quale piattaforma di supervisione per il coordinamento delle attività e la raccolta organica dei dati di processo,Atec Sistemi ha utilizzato Ignition, soluzione software di Inductive Automation, distribuita e supportata in Italia da EFA Automazione.
Ignition è una innovativa piattaforma software che, grazie ad una serie di caratteristiche tecniche uniche nel suo genere, consente di implementare soluzioni avanzate di gestione e supervisione della produzione in ottica di smart factory, ovvero secondo i principi base della digital transformation, che prevede l’integrazione totale degli asset aziendali: sia orizzontale che verticale. Ignition si è rivelata la scelta vincente anche per molti
altri motivi, ad esempio per il fatto che, se l’end-user desiderasse aggiungere altri client di qualsiasi tipo – smarphone, tablet, PC windows o Apple – sarebbe possibile farlo senza alcun problema.
“Il sistema che abbiamo sviluppato su base Ignition dispone di due server ridondati. Alla parte di supervisione e di raccolta dei dati si affianca l’interfaccia, accessibile via web, quindi il database in cui vengono storicizzati i dati e i PLC, che gestiscono in modo diretto le varie partid’impianto, ovvero le macchine che calcolano le rotte. L’apertura offerta da Ignition ha permesso di realizzare un’architettura di produzione completamente integrata con il sistema gestionale. L’operatore può infatti scegliere quale batch attivare e, in automatico, il sistema calcola il percorso per guidare il riso verso la sua destinazione finale”, spiega Ceriani. Al momento in S.P. sono attivi una decina di client, che dovrebbero aumentare a seguito di ulteriori ampliamenti a cui il sistema sarà sottoposto prossimamente”.
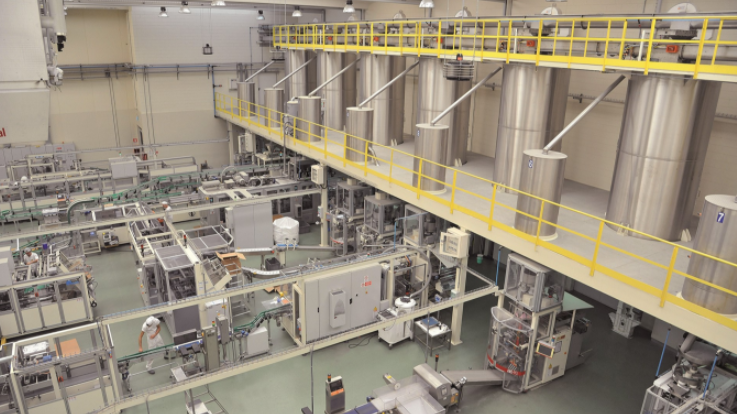
I benefici derivanti dall’utilizzo di Ignition
L’utilizzo di Ignition ha permesso di ottenere notevoli vantaggi.
“Con Ignition siamo riusciti a implementare un sistema capace di offrire una visione generale di tutte le fasi della produzione”, afferma Ceriani. “La possibilità di utilizzare un unico prodotto con il quale gestire tutti gli aspetti impiantistici e di integrazione, sia con il campo che con altri gestionali IT, ha rappresentato un enorme vantaggio, ulteriormente amplificato dal fatto che Ignition consente agli utenti di accedere via interfaccia web”. Benché Atec Sistemi vanti un’esperienza ultraventennale e una serie di progetti gestiti anche a livello internazionale, ogni volta – come ribadisce Mauro Ceriani – è sempre una nuova sfida: per questo, avere al proprio fianco un partner fidato rappresenta una garanzia in più.“EFA Automazione si è sempre dimostrata un partner affidabile, con cui abbiamo un rapporto molto stretto: come anche in altri casi, anche per lo sviluppo di questa applicazione i loro tecnici ci hanno offerto un supporto sempre tempestivo e professionale, che in questo caso,ad esempio, ci è servito per comprendere come gestire al meglio l’interfacciamento della piattaforma con il database di produzione”, conclude Ceriani.